LUOYANG DATANG ENERGY TECH CO.,LTD
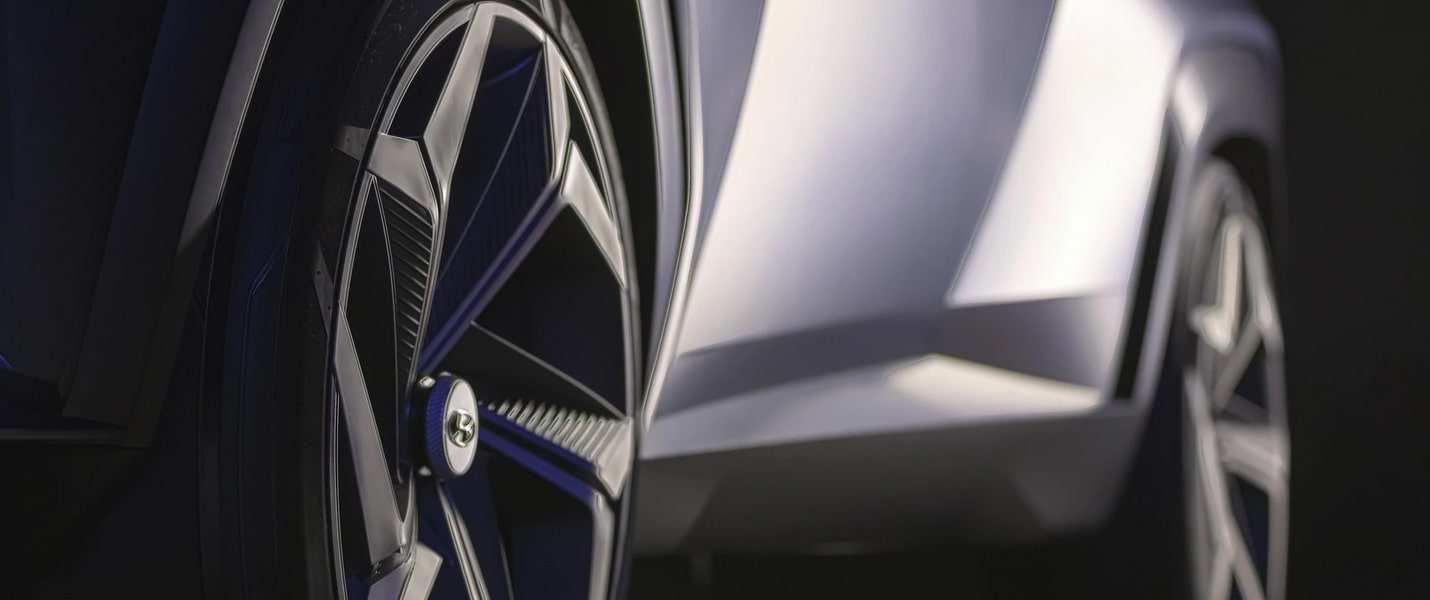
What Fittings Are Used In PPR Pipes? How Are PPR Pipes Joined?
In building water supply and drainage system, HVAC and industrial fluid transportation, PPR (random copolymer polypropylene) pipe and fitting has become the mainstream choice for its corrosion resistance, anti-scaling, long life and other characteristics. However, an efficient and reliable pipeline system not only requires high-quality pipes, but also relies on scientifically designed parts combination and standardized construction technology.
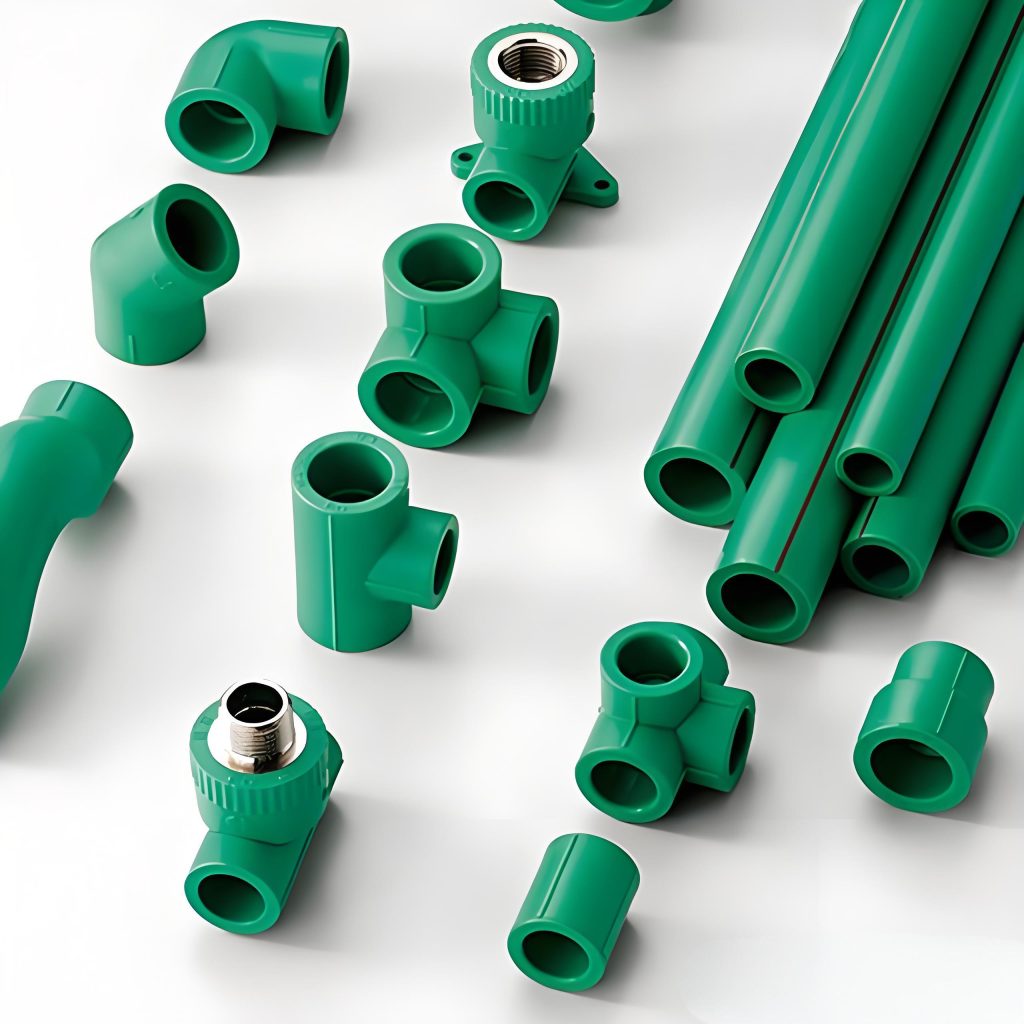
PPR Pipe System Essential Accessories Details
The scientific selection of pipe fittings is the key to ensure the tightness and functionality of the system. The following are the six core fittings classification and selection guidelines:
1. Coupling
Function: linear extension of pipes or repair of local damage
Technical parameters:
Pressure grade needs to match the pipe (common S5/S4/S3.2 series)
Diameter range DN20-DN160, suitable for different flow requirements
Engineering application scenarios:
Extension reconstruction of main pipeline
Quick replacement of damaged pipe section (need to be cut accurately with pipe breaker)
2. 90°/45° Elbow
Hydrodynamic optimization design:
Smooth inner wall transition, reduce the pressure loss caused by turbulence (measured pressure drop <0.03MPa@2m/s)
R =1.5D Large radius of curvature reduces cavitation risk
Installation precautions:
Hot and cold water systems need to distinguish gray/white identification
Support spacing ≤50cm to prevent thermal expansion stress concentration
3. Equal/Reducing Tee
Branch system design points:
The diameter ratio between the main pipe and the branch pipe is ≤0.8 to ensure the uniformity of the shunt
The hot water system preferentially adopts the structure with loose joint, which is convenient for later maintenance
Special industrial applications:
Food grade 316 stainless steel lining tee (acid and alkali corrosion resistance)
Tee with sampling valve (pharmaceutical industry online testing requirements)
4. Flange Adaptor
Cross-material connection solutions:
EPDM rubber seal ring, suitable for -20℃~110℃ working conditions
PN16/PN20 flange pressure rating matching ISO standard
Construction specifications:
Flange bolts should be progressively tightened diagonally (torque values refer to DIN 2501)
Flange surface cleanliness requirements Sa2.5 (no oil, oxide layer)
5.End Cap
Key components of pressure test:
Pressure test value =1.5 times working pressure, holding time ≥30min
Special pressure test cap with pressure gauge interface is recommended
Temporary plugging scheme:
Outdoor pipes should be made of UV anti-aging material (to avoid UV embrittlement)
6. Union
Modular maintenance design:
Quick disassembly structure, supporting tool-free disassembly (patented snap design)
Medical grade system needs to be equipped with no dead cavity sanitary loose joint
Selection calculation:
Rated number of cycles ≥5000 (refer to EN 1254-3)

PPR Pipeline Hot Melt Connection Process Analysis
Professional grade hot melt welding is the core process to ensure zero leakage of pipeline system, and the following standardized operations should be strictly implemented:
1. Preparation stage before construction
Environmental control:
Operating temperature 5℃-40℃, humidity ≤80% (low temperature environment need to enable preheating program)
Set the dust isolation area (cleanliness level ISO 14644-8)
Equipment calibration:
Temperature controller error ±3℃ (check before starting daily)
Mold specification and pipe diameter matching tolerance ≤0.1mm
2. Six-step standardized operation method of hot melt welding
1. Precise cutting
Use a special cutter to ensure that the end face perpendicality is ≤1°
Deburring treatment (45° chamfer recommended)
2 Mark the depth
Set the insertion depth by tube diameter (DN20=14mm, DN25=16mm, and so on)
Use an adjustable scriber to ensure marking accuracy
3. Set heating parameters
Refer to the welding parameter table (example: DN25 pipe, 260±5℃, heating time 7s)
Ambient temperature compensation (±1s/5℃) is required in winter and summer.
4. Synchronous welding
Two people work together to ensure that the pipe fittings advance in sync
Fused ring formation standard: uniform bright no bubbles
5. No stress butt joint
No rotation for linear insertion (deviation Angle ≤2°)
Maintain pressure until end of cooling time (30s for DN25)
6. Quality inspection
Welding seam width detection (standard value: pipe diameter ×0.15+0.5mm)
Profile inspection: the fusion surface should reach 2/3 of the thickness of the pipe wall
Solutions For Special Working Conditions
Small space welding:
Right-angle welding machine (minimum operating space 30×30cm)
Use a reflector to observe the welding state
Working at height specification:
Build welding platform in accordance with OSHA standards
Equipped with anti-fall device and welding torch attachment
PPR Pipeline System Advanced Optimization Strategy
Professional technical solutions to improve system reliability:
1. Hydraulic calculation optimization
Pressure drop simulation using professional software such as PipeFlow
Branch pipe flow rate control: cold water ≤2m/s, hot water ≤1.5m/s
2. Thermal expansion compensation design
Fixed bracket spacing formula: L=0.15×ΔT×α×D
(ΔT= temperature difference, α= coefficient of linear expansion 0.15mm/m·K)
-Ω type compensator setting spacing: riser each layer, horizontal pipe ≤6m
3. Antibacterial pipeline system
Nano silver ion modified pipe (antibacterial rate > 99.9%)
UV disinfection pipe special model (weather resistance grade UV-A)
Why choose our PPR solution?
As a piping system supplier with NSF, WRAS and CE certification, we provide:
Homogeneous tubing manufactured from HAUSEXX production line in Leifen, Germany
100% pressure-tested precision injection molded pipe fittings
15 years warranty
Supplier
Luoyang Datang Energy Tech Co., Ltd. is a leading Chinese manufacturer specializing in high-quality plastic pipes and fittings. Equipped with state-of-the-art automated production lines and supported by a team of 200 professionals, we offer an extensive product line comprising over 150 types of plastic pipes and fittings designed for water supply and drainage systems, gas transmission, and floor heating systems. Our main products include PVC Pipes and Fittings, PE (HDPE) Pipes and Fittings, PPR Pipes and Fittings, and PEX Floor Heating Pipes.
Should you have any inquiries regarding PVC Pipe,PPR Pipe & HDPE Pipe , please do not hesitate to contact us!
Tel.:0086-183 3790 0677
Wechat: 0086-183 3790 0677
Whatsapp: 0086-183 3790 0677
Email: sales@pipesandfittings.net